These are all customized products according to
customer's requirement. If needed, we can
provide custom sevice for you.
In the design of static seals, O-rings are the most widely used. Static seal refers to a seal without relative motion between two adjacent surfaces. If the O-ring size and installation groove size are processed correctly, and the O-ring material is properly selected, the O-ring sealing pressure can reach 100MPa, which can be achieved Zero leakage.
The main reasons for the oil leakage of the static seal of the reducer are:
1) Quality problems of O-rings: O-rings have poor elasticity and surface defects.
2) The O-ring is trimmed due to assembly; or the tightening torque of the connecting bolt is insufficient.
3) The processing quality of parts and components.
Treatment measures:
1) Select qualified O-rings produced by regular manufacturers.
2) Make sure that the connecting bolts should have sufficient strength to avoid gaps on the joint surface, causing the O-ring to be squeezed out by pressure and leaking oil.
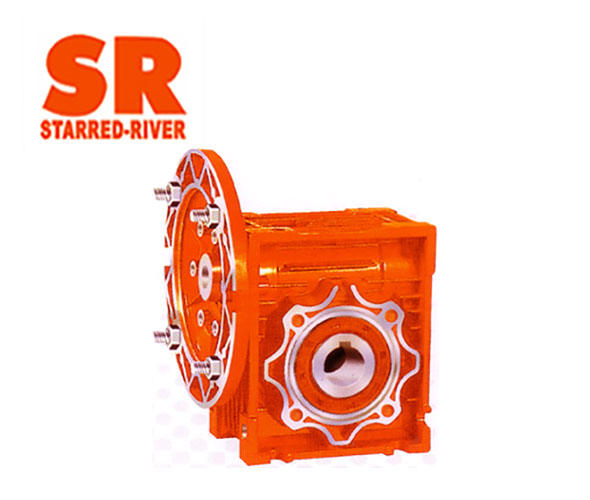
O-ring seal design:
a) Guide cone requirements: Since the O-ring is squeezed during installation, the edges and corners of the guide cone must be designed to be rounded to avoid surface extrusion and seal failure of the O-ring. The guide cone should be between 15° and 20°. Please refer to the standard GB/T3452.1-2005 O-ring seal groove size and tolerance for the width of the guide cone.
b) Groove design: Groove design includes determining the shape, size, precision and surface roughness of the groove.
Design principles: easy to process, reasonable size, easy to ensure accuracy. The common groove type is the rectangular groove. The advantage of this groove is that it is easy to process, and it is convenient to ensure that the O-ring has the necessary compression. In addition to rectangular grooves, there are grooves in the form of V-shaped, semi-circular, dovetail and triangular.
3) Reciprocating seal
In hydraulic systems, reciprocating seals are one of the most common sealing requirements. The reciprocating motion seal is used between the piston and the cylinder in the reducer brake to limit the axial leakage of hydraulic oil. When used as a reciprocating seal, the pre-sealing effect of the O-ring is the same as that of the static seal, and due to the elastic force of the O-ring itself, it has the ability to automatically compensate after wear.
The most common type of failure is twisted O-rings. Twist is the phenomenon in which the O-ring is twisted in the circumferential direction. There are many reasons for twisting damage, the most important of which are the machining accuracy of the sealing parts (including clearance, coaxiality and roughness), as well as the coaxiality deviation of the sealing groove, the unequal sealing height and the O-ring section Uneven diameter, etc.